The First Paper Published by China Authoritative Magazine
The China Building Materials 2018, 2nd issue
Thinking and Application of New Nucleated Material in Cement Industry
1. Preface
New Nucleated Material(NNM)------a special abrasion-resisting material developed by Jingniu, is of good performances of abrasion resistance, temperature resistance, corrosion resistance and thermal stability. Experiment in cement equipment is made to extend service life, reduce power consumption and operate safely. In most cases, NNM can replace abrasion-resisting alloy, cast stone, ceramic tile and castable, and is applied to work conditions that are washed against hot-air and materials with usage temperature of 800℃ and above, as well as resist alkali, abrasion and heat and impact by materials. The specific experiment places include the second bin lining of ball mill, the fourth and fifth internal cylinders of preheater, flue chamber of calciner and side wall of grate cooler. Experimental period is one year.
2. Advantage analysis to NNM
NNM ---- a compound-phase abrasion and corrosion resisting material based on CNSi (new nucleated material, NNM). The prime materials include silicon carbide(15%~33%), silicon nitride(4%~12%), zirconium silicate (20~50%), quartz(10%~15%), glass-ceramic powder(4%~8%)、 glass beads(3%~7%), It is made by slip casting or pressing formation of base and then by a single sintering process at 1400~1500℃, and finally it becomes a compound-phase abrasion resisting material of combining microcrystalline silicon nitride and silicon carbide.
⑴. Light weight: as a substitute for alloy lining of the second bin of ball mill, and on the condition that original property is kept, density of NNM is only 2.7-3.0g/cm
3, one-second of that of alloy steel. Overall weight of ball mill will be reduced if lining volume is same. Usually cement mill ofΦ4.2*13 is used in cement plants, its total weight of the second bin lining is about 33.39 ton if alloy steel lining is installed. If alloy steel lining is replace by NNM, the weight can be lowered by 20ton.
Costs of cement production mainly include coal, power, raw materials, depreciation and the others, of which power takes up about 27% of total cost. Power consumption and power cost can be lowered by reducing electrical load of ball mill if alloy lining is replace by NNM.
⑵. High temperature resistance: operation temperature of NNM is 1200℃, reaches to 1300℃ in short time and performance will decline along with increasing temperature. Properties of abrasion resistance and high-temperature resistance have offered good applications for NNM, it is especially applicable to cement plants’ tough environment of high temperature, dust, washing against wall and frequent maintenance, like internal cylinder No.1 to No.5 of preheater, flue chamber of calciner, part one of grate cooler and tertiary flue
⑶. Good thermal stability:Thermal stability means property of thermal shock resistance. thermal stability of NNM depends on its thermal expandability, thermal conductivity and breaking tenacity, as well as its structure, shape and size. Its thermal shock test is carried out at 750℃ with water-cooling times>10, actual temperature is interactive between 1200℃ and 100℃ without damage. NNM can be a substitute for castable, its excellent thermal shock resistance makes it applicable to level1 to 5 of preheater, part 2 and 3 of grate cooler pipes of kiln and separator in cement industry, extending equipment service life and enhancing productivity.
⑷. high abrasion resistance: abrasion-resisting property of NNM is superb, its abrasion loss is 0.03 g/cm
2, so abrasion resistance of NNM is as three times as that of cast stone(0.09g/cm
2). As a substitute for cast stone, ceramic plate, white pig iron and overlap welding, it is suitable for lining plate of mill, chute and silo wall in cement industry.
⑸. Acid and alkali resistance: NNM is an inorganic nonmetal material, its corrosion resistance is better than alloy, ceramic tile and castables. It is both acid and alkali resisting even at high temperature. Its performance of acid and alkali resistance is as follows: dense sulfuric acid 99.61%, dilute sulfuric acid (20%) 99.44%. NaOH solution (20%) 96.38%. Its corrosion resistance is superior. Instead of castable, NNM won’t react with cement raw meal at high temperature and it is effective to prevent crusting. Experiment result is promising, productivity is enhanced, labour intensity reduced and production accidents decreased.
3. Application experiment of NNM and its result in cement industry
⑴. NNM is used as lining plate of cement ball mill: Lining plate of ball mill is mainly used to protect cylinder from impact and abrasion by materials and grinding medium. In the meantime motion state of grinding body in each bin can be adjusted by using different kind of lining plate. It is always the pursuit of increasing output and reducing consumption to develop new abrasion-resisting lining, ball and create the best working condition of ball mill.
NNM lining plate is tested in Handan Jinyu Taihang cement plant, the requirement of lining plate is abrasion and impact resisting and without falling off. The experiment lasts for one year (from Oct. 27, 2016 to Sept. 30, 2017). Two kinds of NNM are tested, the first generation and the second generation. The type of cement mill is Φ4.2x13m, two-bin grinding belt, 160-140 roll press grinding system. The size of alloy lining plate is 304×242×62/47mm with a piece weight of 26.50kg. The total number of lining plates in the second bin is 1260 with total weight of 33.39t. The number in the first bin is 402 with total weight of 12.06t. In the experiment some alloy lining plates are replaced with NNM lining. The size is the same 304×242×62/47mm. the average piece weight of NNM lining plate is 10.84kg, 15.66kg of weight is reduced each piece.
NNM lining is installed to the surrounding area of the second bin gate of No.6 cement mill, as shown in drawing 1. On Oct. 27, 2016, twenty pieces of the 1
st generation NNM lining plate and one test lining plate of the other material are installed, observed and tested every month. On May 22, 2017, eight times are measured to the thickness of checkered plate, and there is certain abrasion to the ripple, up to 3mm. The result is not satisfactory. So four pieces of the 2
nd generation NNM are installed to the north of the gate to replace the 1
st generation NNM, Observed and tested continued. After 4 measurements the depth of ripple remains 15mm without fracturing and abrasion. The effect is better than the 1
st generation NNM lining. Up to Sept. 30, 2017 the 1
st generation lining plates in No.6 cement mill have operated for 2329.2hrs, producing cement of 427265ton. The 2
nd generation lining(4pcs) 854.9hrs, producing cement 142051ton. Service condition and measurements of NNM lining plate are shown at drawing 3 and 4.
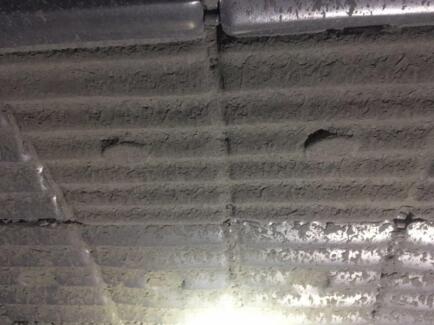
Drawing 1NNM just installed to No.6 mill in Jinyu Drawing 2 two months operation in No.6 mill
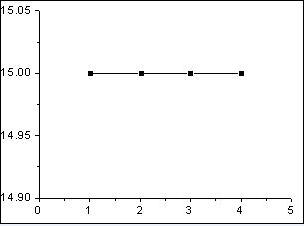
Drawing 3 plate thickness of 1
st generation NNM Drawing 4 thickness of the 2
nd generation NNM
Compared with alloy plate, NNM lining plate is lighter and better in abrasion resistance. For example, the second bin is installed with NNM lining, mill weight is reduced by 19.73 ton, power rating of mill main motor is predicted to reduce by 200 kW. Power consumption per ton of cement can drop 1.1kWh/t. For example, if the second bin lining plates of the 3 cement mills of Jinyu Taihang cement are replaced with NNM lining, it is predicted that 2 310 000kwh of power or some RMB 1 200 000 yuan can be saved.
Up to now the 2
nd generation NNM lining has been safely used for 14 months in Handan Jinyu cement plant, it is still perfect and meets requirements of production process. To replace alloy lining with NNM lining can reduce power consumption and emission of greenhouse gas, and bring about great economic and social benefit.
⑵. NNM is installed to internal cylinder of preheater that is one of the main machine of cement plant, preheater and calciner constitute kiln inlet system which achieves decomposition of calcium carbonate outside kiln. If attention to preheater and calciner is not enough and lining material unsuitable, shortcomings and accident will emerge like crusting, blocking, collapse, high local temperature, low running rate and poor clinker quality.
Preheater is usually composed of 4 or 5 levels, operation temperature of level1 to 3 is between 300-800℃, level4 to 5 800℃ and above. Operating environment of preheater is often washed by materials and heated wind. Therefore its lining material shall be abrasion resisting, high temperature resisting, acid and alkali resisting and thermal shock resisting.
Experimental location: part of flue chamber of No.3 kiln Zanhuang Jinyu cement plant.
Case parameter: kiln type: Φ4.4*52m, two-level short kiln. Five-level two-system preheater is designed by a Tianjin institute. Temperature of flue chamber is 1150-1250℃.
Conditions before application: flue chamber crusts severely and its thickness increases 2-3 cm per hour. Usually it needs to clean 3 times each shift (8 hrs).
Purpose of substitution experiment: high temperature resistance of NNM>1300℃, and the experiment is to test whether NNM surface has crust resisting property. The position of the experiment is the one sq.m south wall of flue chamber where castable is replaced with NNM lining plate. The lining plate is installed and castable is fully filled and maintained.
Conditions of monitoring and inspection: on July 5, 2017 NNM lining was installed and on July 9 put into operation. Experimental conditions are as follows: A. observing whether the installed NNM is any breakage or crusting resistance after normal material feeding. Cleaning to this place stops. No breakage and crust to NNM lining plate is found after 8 hours. B. no thick crust is found after one week. C. On July 26 when production stopped, there is no damage or fracture in the lining plate found. There is only a layer of 0.5-2.0 cm crust on surface. Cleaning the crust is simple and it falls when blowing.
Experimental result proves: ⑴. The lining plate installed to preheater in cement industry and its high temperature resistance can meet production requirement (>1300℃). There is no falling off or firing crack occurred. ⑵. There is only 2 cm crust on the lining plate after 17-day operation and without cleaning during the period. The crust is easy to clean and the requirement of crust resistance is achieved. ⑶. It needs to clean crust three times during each shift and the heavy and dangerous artificial work strength is greatly reduced. The application drawing is as follows:
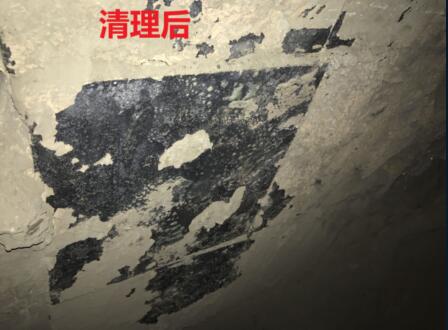
⑷. Installed to side wall of grate cooler
Grate cooler is important equipment in clinker burning system of cement plant and its function is to cool and transport clinker. In the meantime it supplies rotary kiln and calciner with hot-air and is a main equipment to recycle heat of clinker burning system. Air quenching cooler is a shock cooling cooler, its output reaches to 600~10000t/d and it can cool 1370℃ clinker to below 100℃ in several minutes with clinker granularity≤25mm, and siding wears out severely. The condition of grate cooler at operation is washed against materials with hot-air. Therefore grate cooler should be acid and alkali resisting, abrasion resisting, thermal insulation, high temperature resisting and some area impact resisting. Normal operation is seriously affected due to high maintenance cost and long repair cycle of grate cooler. Requirement to grate cooler siding shall be high temperature, abrasion, thermal shock, acid and alkali resisting so as to lessen abrasion and failure rate, prolong service life, reduce maintenance cost and enhance productivity.
The experiment that NNM, instead of castable, is installed to sidewall of grate cooler is carried out in Zanhuang Jinyu Cement Company. The application effect is shown in drawing 5-8.
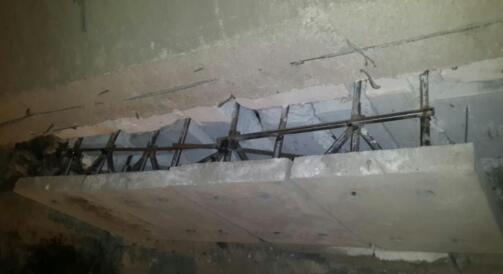
Drawing 5 before NNM is installed Drawing 6 installing NNM
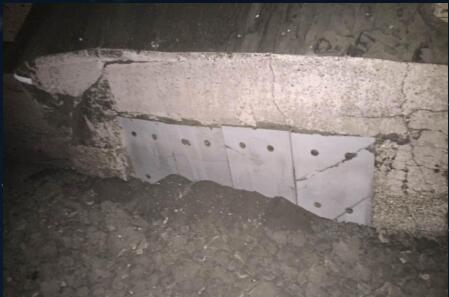
Drawing 7 after NNM is installed Drawing 8 after NNM running two months
Note: those with holes are NNM, the surrounding is abrasion resisting castable used before.
The experimental result finds that after NNM lining plates are installed to sidewall of grate cooler, they are running smoothly except one piece that crack occurs. Basically there is no abrasion, breakage, falling, collapse and burning loss emerged. There is a good application prospect for NNM lining plate in cement industry.
4. Summary and thinking
⑴ Summary: owing to the property of abrasion resistance and thermal shock resistance, NNM developed by Jingniu, as lining plate, has been applied to grinding system, sidewall of grate cooler, cylinder of preheater, pendant, shutter, chute, weighing loophole and triple air-lock gate of vertical mill of cement industry with very good effect.
⑵ thinking: the reason why NNM has properties of abrasion, high temperature, corrosion resistance and good thermal stability and is suitable to place that is crusting easily and needs property of abrasion and high temperature resistance in cement industry is related to crystal structure, quality of raw materials and special process control.
A: NNM is a dense sinter that is composed of silicon carbide and silicon nitride. SiC is a covalent compound that covalent bond is main force to bind atoms. When carbon and silicon forms SiC crystal, S→P electron of SiC atom migrates and leads to SP3 hybrid arrangement with stabilized energy. Consequently the structure of SiC that is similar to that of diamond, regular tetrahedron, is formed. It is of high hardness(Moh’s hardness 9.3-9.5)and stable property. Its physical property is similar to diamond. Silicon nitride(Si3N4)is also a covalent compound, hexagonal system. The crystal structure of Si3N4 is that Si atom forms covalent bonds with surrounding 4 N atoms and constitutes a Si3N4 tetrahedron structure. All tetrahedrons share vertex angles and constitute tree-dimension space networks. Silicon nitride is a covalent compound with strong covalent bond and good chemical stability, and won’t be oxidized below 1200℃. Just because that there are silicon carbide(SiC)and silicon nitride(Si3N4)tetrahedron structures existing, NNM possesses superior properties in strength, hardness, abrasion and corrosion resistance.
B: selection of raw material and reasonable granularity: main raw materials include silicon carbide, silicon nitride, zirconium silicate, quarts, ceramic powder and glass microbead. Of which silicon carbide(SiC)is of chemical stability, high thermal conductivity, low thermal expandability and good abrasion resistance, its sintering temperature is 2000℃; Silicon nitride(Si3N4)is a superhard material with properties of lubricity, abrasion resistance, antioxidation at high temperature, thermal shock resistance and without breakage when it is heated to over 1000℃ and cooled and heated sharply; Zirconium silicate is of chemical stability, its performance is not affected by sintering atmosphere, it can remarkably improve binding ability of roughcast of NNM and enhance hardness, strength and abrasive resistance. Based on features of the above materials, substrate of silicon carbide and silicon nitride, reasonable granularity and sintering at 1400~1500℃, a special abrasion resisting material----New Nucleated Material(NNM) is formed that combines excellent features of silicon carbide and silicon nitride with properties of high temperature, thermal shock resistance and high strength.
C: high strength binding agent is added to NNM to solve bonding problem among silicon carbide, silicon nitride and zirconium silicate, and effectively reduce sintering temperature. Glass beads are tiny balls which have a better flowability than flake, acicular, regular fillers in liquid resin; therefore they have good molding performance. Furthermore glass beads are of the same nature in each direction with nice dispersibility and flowability, and they won’t lead to different shrink rate due to different tropism and stable size is ensured. Problems like shrinkage, deformation and fracture of roughcast during drying and burning are solved. They are used to produce large and irregular products.
D: sintering process usually uses power or natural gas as its energy, single sintering process is more difficult, requirement more demanding and cost higher, but quality is higher, too.
In short: the writer regards that NNM lining with excellent property can be reasonably applied to working conditions of cement plant that is washed by hot-air and materials, and those areas that require acid and alkali, abrasion, heat and impact resistance with operating temperature of 800℃ and above. The applications are reformatory and exemplary to production cost and process quality, and will make a big contribution to improve production cost, save energy, reduce cost and operate safely in cement industry.